Overmoulding Capabilities
We use a range of overmoulding processes to achieve the best possible outcome, both in terms of ergonomics and aesthetics.
Different methods have their own distinct advantages and we can help to support customers with recommendations for the best overmould process for their cable and connector products.
Application Story - Creating Custom, Waterproof Connectors Through Overmoulding
Single shot, high pressure moulding
The high pressure moulding process involves injecting material into a mould in cycles, under high pressure (up to 2000 bar, compared to up to 5 to 40 bar for low pressure moulding). This is the most common overmoulding process for GTK.
The first cycle is the inner mould, which is a lower pressure, lower temperature mould process. The reason for this process is to protect the solder joints, and any components used inside the moulded area. It also holds everything in place, and prevents wires being too close to the surface of the overmould, ensuring a consistent thickness of overmould material.
The second cycle is the outer mould. The chosen mould material is injected at a higher pressure and temperature, which ensures that the mould material spreads to all corners of the mould tool, and where required, bonds to the cable jacket.
The choice of material used for the outer mould includes PVC, PU, and PE. Our customers can also choose from a wide range of Pantone matched colours and can specify shore hardness dependent on requirements. Logos or embossed labels are incorporated at this stage to ensure cohesive branding across your chosen products.
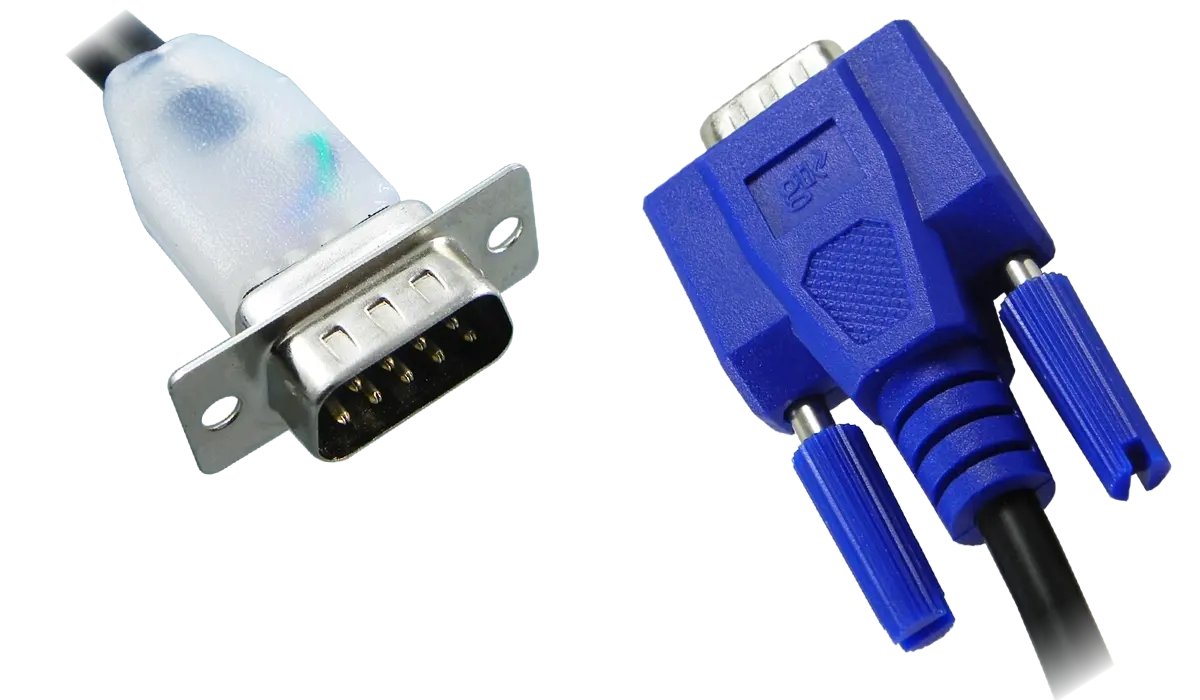
Insert Moulding
Insert moulding isn’t just typical overmoulding. Instead of overmoulding directly on to the connector, the mould material encases the wire and contacts directly, without the need for a connector housing.
Contacts are soldered to the wires and then held in a jig to keep the pitch, coplanarity and relative position of the contacts. The jig is then inserted into the mould machine, with the mould material forming part of the mating face of the connector around the pins and wiring.
In this process it is important to ensure that the shore hardness of the mould material is correct. Too soft and the mating face is malleable and may cause mating issues; too hard and it can be brittle.
Pictured here, the black mating part of the connector is formed at the same time, and from the same mould, as the black material behind the silver locking ring.
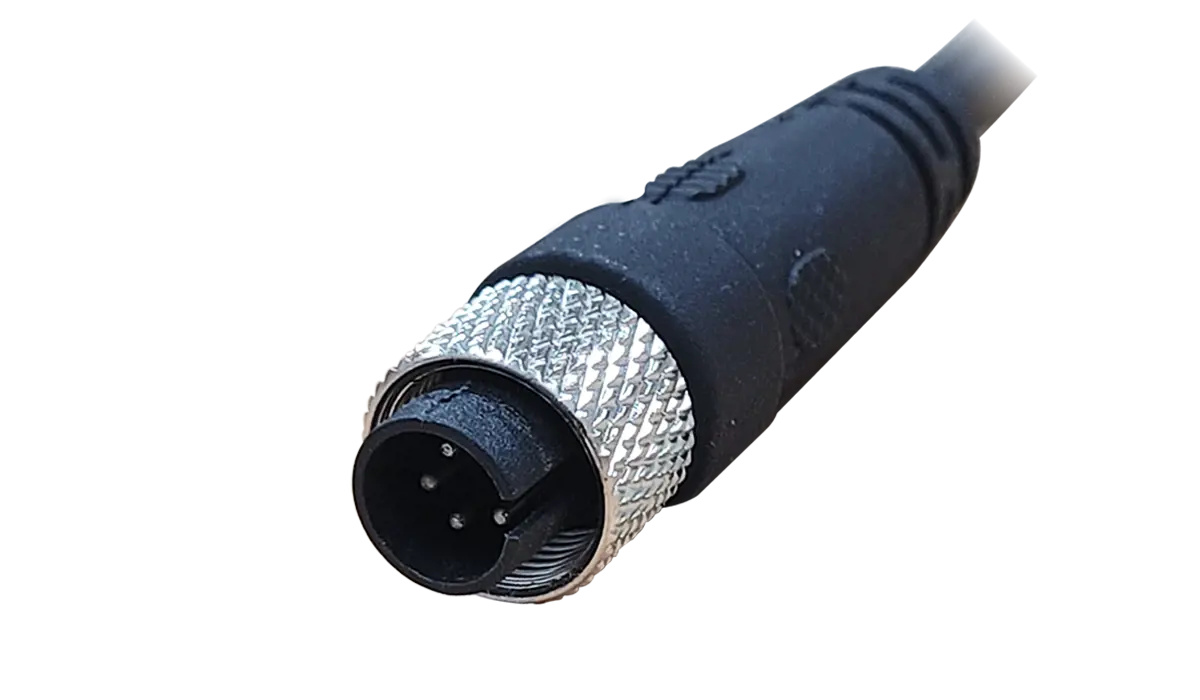
Multi-shot Moulding
Multi-shot injection moulding uses the same process as single shot high pressure moulding, however the overmoulding machine has two or more barrels, allowing two materials of different colours or types to be shot into the mould during the same cycle.
This is often used in consumer electronics as a way to differentiate products from others on the market, or to incorporate two company colours into a single connector product if this is a key requirement.
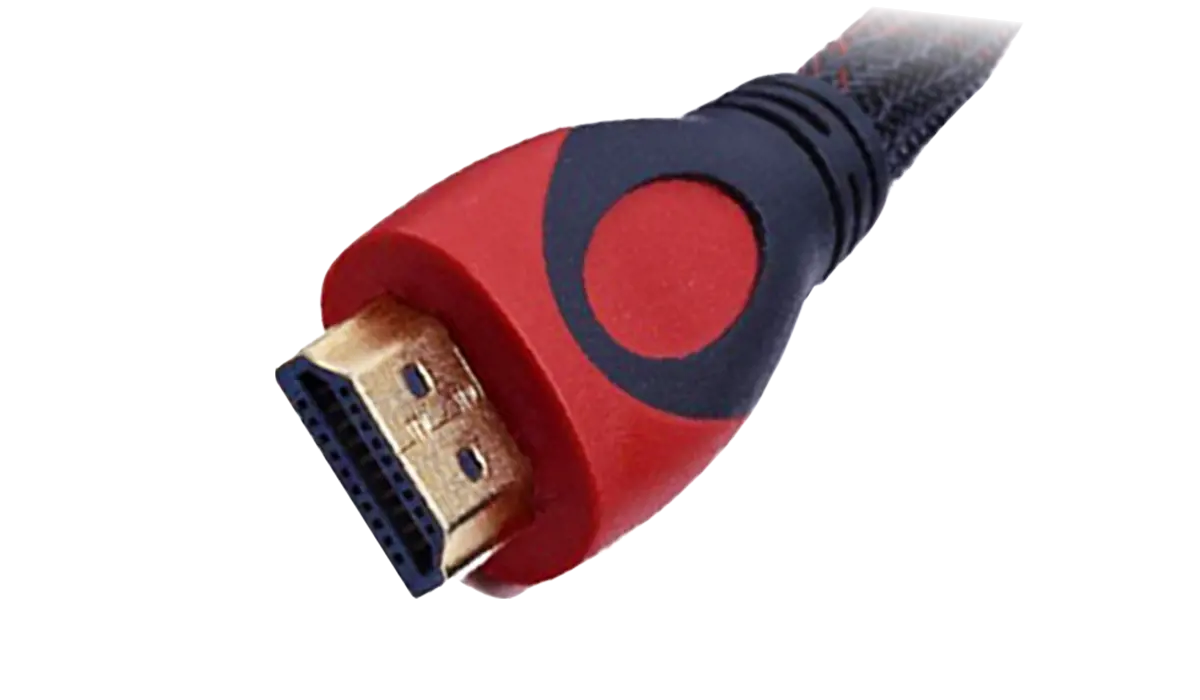
Low Pressure Moulding
Low pressure injection moulding is used to protect electronics from moisture, dust, dirt and vibration. Where low pressure moulding is particularly useful, is to encapsulate more fragile electronic components.
It operates at a lower pressure, typically between 5 and 40 bar, compared with up to 2000 bar for standard injection moulding processes.
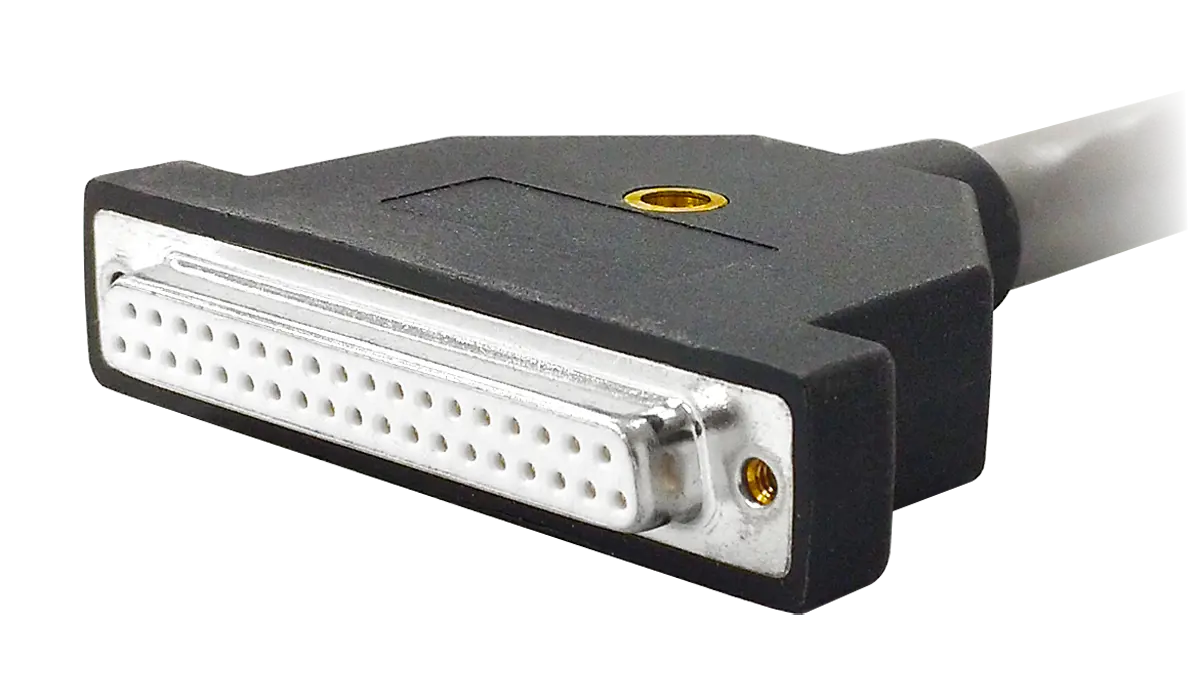
Moulded Strain Reliefs
Where necessary, our products incorporate the highest quality moulded strain reliefs. These strain reliefs are used to protect the area where the flexible cable meets the stiff connection point, protecting the cable from mechanical forces and ensuring that there is no damage or compromise in performance.
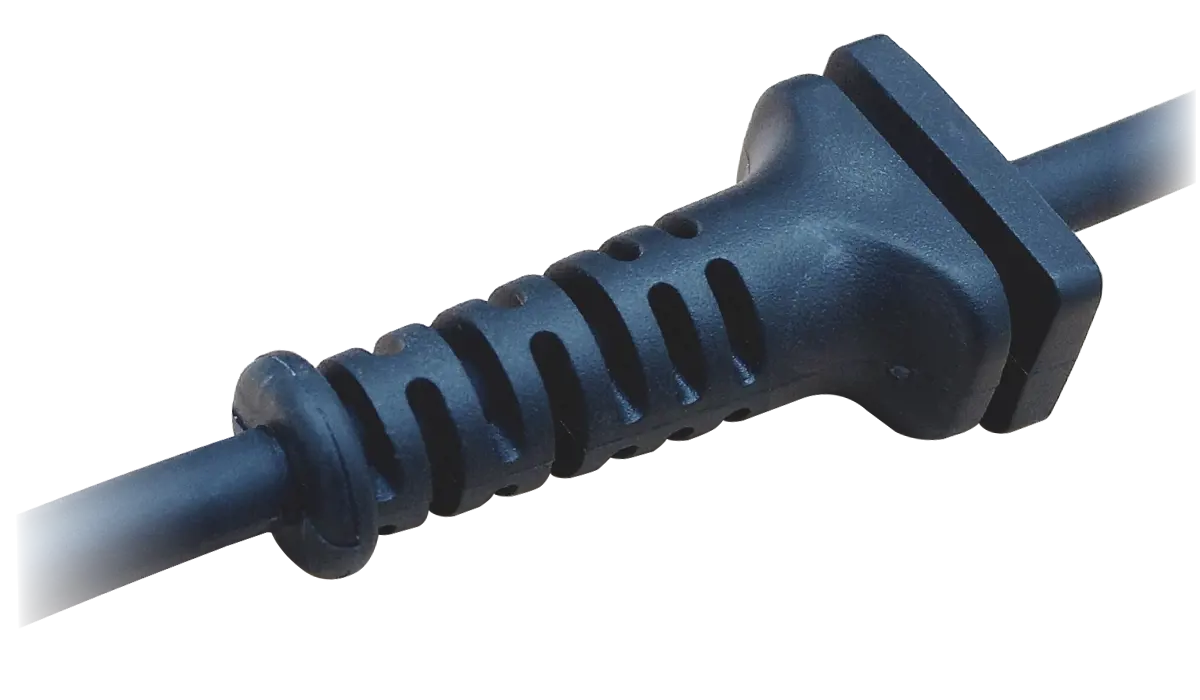